The safe and timely arrival of goods is important for many businesses across Australia. However, over recent months the team at NTI has seen a marked increase in cases of water damage to goods while being shipped via sea voyage.
As well as goods damaged in transit being a source of frustration for the importer and exporter, goods damaged in such a way during their transit has a major knock-on effect on the receiving business.
From increased administration, reordering goods, increased lead times, product recalls and loss of sales, damage such as this can cause an unwanted – and often unnecessary – headache for businesses.
“It can also put strain on contracts and agreements down the line if, for example, a construction contract is delayed because of damaged materials,” says Antony Wong, Marine Claims Manager at NTI.
“This is one example of how the world of shipping and global trade is changing, and it’s important that brokers and clients keep up to date with these issues to help minimise and manage the risks they present.”
Why has water damage in container cargo been increasing?
There are a number of issues driving up the frequency of water damage in container cargo this year, some of which are unavoidable, others which can potentially be managed. Some of the issues result in damage from water entering containers, while damage is also happening due to poor moisture management. Let’s take a closer look at the issues, and how they can be addressed.
Geopolitical troubles causing delays
We’re all well versed in the conflict happening in Ukraine, Russia, Israel and Palestine, along with political unrest in other regions and the impact this is having on global shipping. For example, current issues in the Red Sea have resulted in cargo vessels travelling around the Cape of Good Hope. This adds significantly to the time goods are spending at sea, and therefore increasing the potential for loss and damage.
Solution: Unfortunately, there’s no direct solution to the root cause of this problem. However, understanding that goods are likely to spend more time at sea, the need to address the following issues is essential.
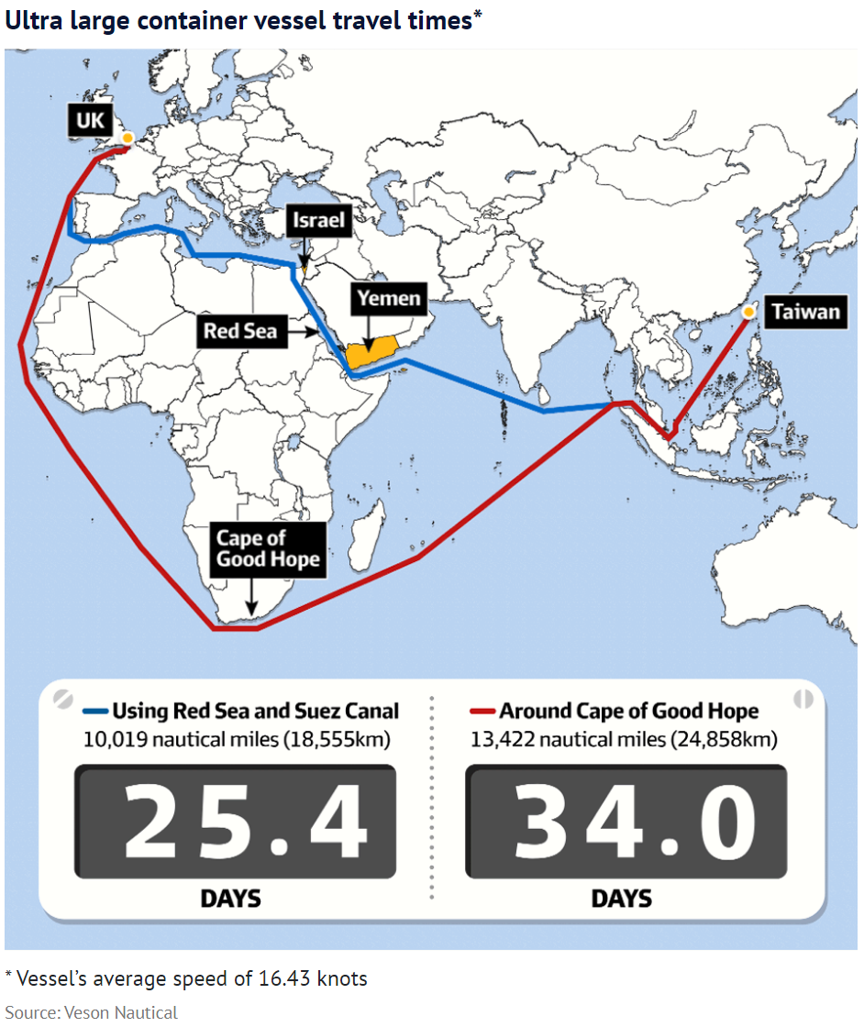
Insufficient quality containers available
Shipping demand has stabilised after the pandemic highs, but it remains high – which increases pressure on the containers being used globally. That demand means containers that have previously been decommissioned are being brought back into use, and others are being used for longer periods than before.
“Understandably, the problem with these containers is that they are not in the best shape,” says Chelsea Neely, Logistics Risk Engineer at NTI.
“What we have seen in many of these containers is that they have one or multiple issues - faulty seals, holes from wear and tear, and repair chalk falling off.”
This, of course, can result in water-damaged goods, either from sea water making its way into the container, or moisture building due to the conditions inside the container.
Poor ventilation is also causing issues – “Container vents may have been taped during previous journeys if they’d been used to transport bulk goods like grains, but for many products it’s important they’re left open for passive ventilation” says Chelsea.
Solution: A business can request the carrier or freight forwarder inspect the container prior to shipping, noting particularly any signs that water damage could be a risk such as visible wear and tear or obvious gaps or holes where light is entering the container.
Substandard packaging used
Often, goods haven’t been packaged well enough to protect them from damage.
For example, when inadequate timbers – either green timber or wet wood that’s been exposed to the elements – are used as packing, the wood can contain moisture which can release into the container.
“We have also seen an increased number of shipments in the last few months that do not have sufficient desiccant bags that absorb moisture – and in some cases none at all.”
Packaging can sometimes be influenced by environmental, social, and governance (ESG) concerns. However, many sustainable options now exist, such as desiccant bags made from desiccant clay, which is non-toxic and recyclable.
“For most cargo types and depending on the type of desiccant, 8 to 12 bags/poles are required in a 20ft container, and 16 to 24 are required in a 40ft container,” says Chelsea.
Solution: The responsibility here lies with the party shipping the goods or the freight forwarder. However, it’s important the receiving party asks the right questions to ensure cargo is being packaged correctly and in line with the freight forwarder’s moisture management plan.
Lack of moisture management plans
“Within a container, heat builds, and if there’s moisture in there too it can create a humid, rainforest-type environment, which can cause significant damage to goods and products,” says Antony.
This issue is prevalent in Australia, as most shipments come from or through Asia, where the weather is hot, humid and going through their wet/monsoon season.
Freight forwarders and carriers should have a moisture management plan they are working to.
Solution: A moisture management plan is essential when shipping cargo – and should include the following:
- Consider the use of desiccants, de-humidifiers and insulation.
- Before placing cargo in storage containers, ensure cargo is dry – this includes packing material. Often pallets and timber packaging have been stored unprotected, exposing them to the elements. Therefore, they likely have absorbed moisture prior to shipment.
- Inspect containers prior to usage for holes and damage to prevent water from entering.
- Reduce weather exposure of equipment if possible – storing containers undercover, inside and in a moisture-free environment.
- Check container vents – often vents can be taped up from previous shipments which prevents passive ventilation taking place.
- The condition of the vessel. If possible, inspect the manhole cover condition. Water can enter holds from ballast tanks or bilge systems.
Bring the experts onboard
Water damaged cargo is just one of the many unique challenges NTI’s Marine specialists work on with brokers and clients to ensure goods are transported safely and reliably across Australia and beyond.
Bringing together a wealth of experience from technical marine underwriters, marine claims specialists, internal recoveries experts, and in-house risk engineers, the team has a deep understanding of the vast array of challenges and considerations when shipping cargo.
To learn more or discuss further, contact your NTI representative today.
This article contains general information only.