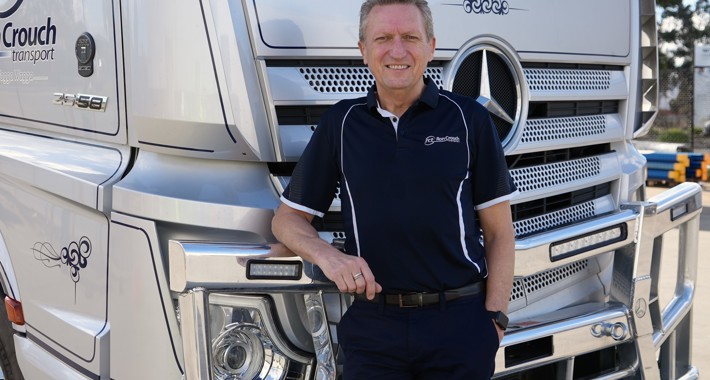
Managing fatigue: cost vs benefit
Too many transport businesses are hesitant to invest in fatigue management technology, such as driver monitoring systems (DMSes). Why? All too often, it’s because they don’t think there’ll be a return on investment.
However, the business case for fatigue management is straightforward: the cost of installing monitoring systems is far less than the cost of the incidents they’ll prevent.
“It’s better than paying the excess [on a claim],” says Ron Crouch Transport’s Executive Director, Geoff Crouch.
“It costs much less than the grief of losing someone. Much less than reputational harm, the trouble you go through with your customers if you have to tell them you’ve lost $200,000 worth of their cargo.
“It’s a classic false economy. It just doesn’t add up.”
Driver management systems
DMSes generate value by proactively managing fatigue. When it detects a fatigue or distraction event, it triggers alerts in the cab, such as an alarm tone or seat vibrations. It also triggers notifications at the depot.
The in-cab alarms should bring the driver’s attention back to the road and signal that they might need a rest stop. The at-base notifications are logged for later investigation.
You can then analyse these notifications. They’ll help you identify fatigue ‘black spots’, optimise routes and schedules, and give your drivers confidence that you’re looking after them.
Deployment and calibration
Drivers often resist DMSes because they believe they’ll be under surveillance. Adam Gibson, NTI’s Transport and Logistics Risk Engineer (and 2021 NTARC report author), says that “the key here is early, honest and, critically, two-way communication”.
Deployment is critical. You’ll have wasted your investment in safety systems if your drivers are actively circumventing them. Adam notes that “some drivers have the misconception that the technology is going to allow operators to look at everything they’re doing in the cab.”
“Nothing could be further from the truth. The algorithms only generate alerts and record footage when they detect a fatigue event.”
Ron Crouch Transport had a successful trial rollout, which Geoff puts down to the company’s investment of time and effort to get the drivers involved in the trial and onboard.
“We had a slow process over 12 months of continually reinforcing the message and talking to our drivers, calling out the benefits,” he says.
“Most importantly, we continued calling out the misconceptions and reinforcing the positives.”
Once the data starts rolling in, make sure your alerts are useful. Getting too many is just as bad as getting too few. You many need to adjust tolerances and trigger times, such as for how long a driver can look away from the road before triggering a distraction event.
Worst- and best-case scenarios
The worst-case scenario is that rolling out a DMS causes drivers to leave, meaning you have trucks sitting idle.
“You can’t give in to unreasonable driver demands or threats,” Geoff says. “If worst comes to worst, you’re better off with a truck parked up in the depot while you try to fill the seat.”
“That’s better than having it parked up because there was a crash, and you’re trying to buy a new cab and get new trailers built, especially with things the way they are now.”
The best-case scenario, on the other hand, has benefits for operators and drivers alike. On the operations side, fewer incidents mean you save money on maintenance, repairs and even insurance.
For some drivers, an unexpected benefit has been a sleep apnea diagnosis. Many drivers fear that a diagnosis will end their career, but it doesn’t make financial sense to lose a driver when the cure is so effective and costs so little.
“The reality is that for most drivers, if they get diagnosed, they get treatment to manage their sleep apnea. Then their quality of life improves out of sight,” Adam says.
Risk management 101
Fatigue crashes are avoidable, and the cost-benefit analysis is squarely in favour of DMSes.
However, there is another way to think about how you manage fatigue risks.
“If you do it well, it becomes a competitive advantage,” Geoff says. “More and more big companies want to see that you’ve got fatigue management systems in place.”
“If you can’t tick that box, then you’re out.”
Ultimately, Geoff thinks fatigue management systems are likely to become mandatory, just as logbooks and other measures have.
“It’s not a matter of ‘if’, it’s a matter of ‘when’,” he says. “Eventually, a politician or a regulator is going to put the case forward, and the industry will have to respond.”
When that day comes, you’ll have two choices: “You’ll either be on that path, doing it in a controlled way that suits your business, or you’ll be doing it in a mad scramble at the last minute.”
Which situation would you rather be in?
- This article is part of NTI’s The Business of Safety series, funded by the NHVR’s Heavy Vehicle Safety Initiative, supported by the Australian Government. For more info, visit nti.com.au/better-business-hub/business-of-safety. Information in this article is a guide only. It does not take into account your personal or business circumstances. Whilst all due care has been taken, you must not rely on the information as an alternative to legal, legislated regulatory and compliance requirements associated with your business activities. NTI.M002.10.27072021